FPC 是用柔性的绝缘基材制成的印制线路板,跟硬板相比具有许多优点。比如配线密度高、轻薄、可自由弯折、可立体组装、成本低,在产品的造型设计和可靠性设计方面有明显的优势。
汽车 FPC 主要应用领域包括车载显示器群及车用电子设备,发动机系统,座椅、车门、车控等电控自动系统,汽车影像系统及传感器等自动安全系统,每辆车需要 FPC 大约 100片以上。
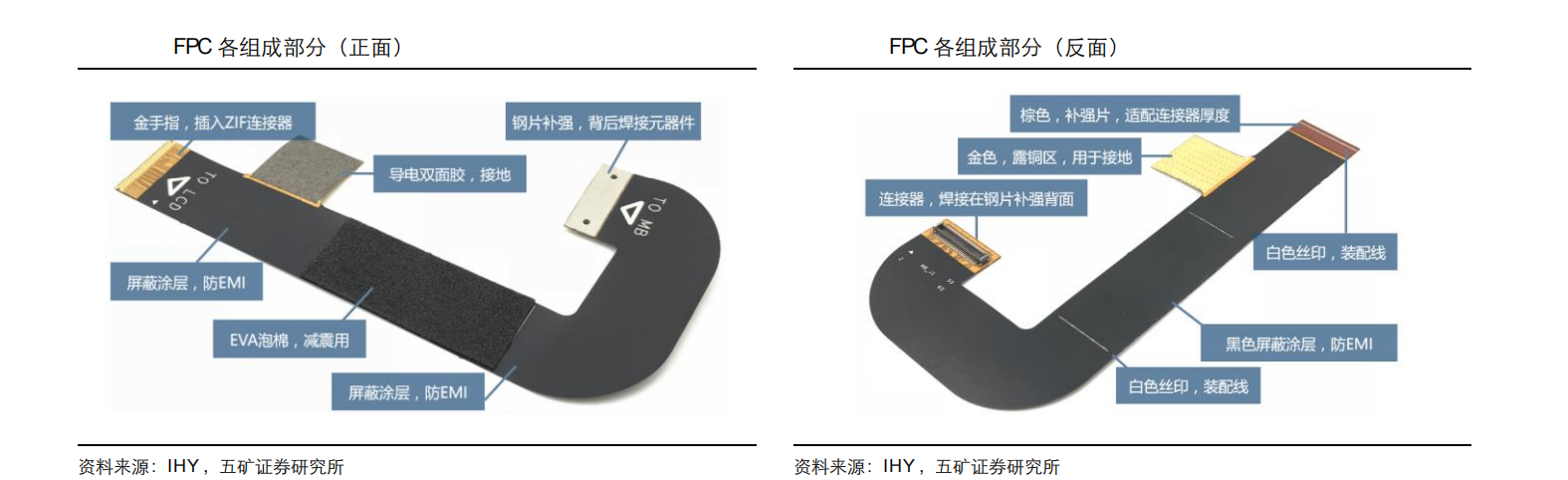
随着新能源车渗透率快速提升,动力电池厂商需要提高电池能量密度和安全性、提高生产效率,以降低产品成本提高整体竞争力。其中在线束方面,用 FPC 替代传统线束,成为动力电池企业在电池 PACK 新材料导入方面的可行性选择。
传统线束主要有铜线和外部的包围塑料组成,几股线包成绝缘体形成一根线束,连接电池时每一根线束要连接一个电极。而当电流信号很多时,需要多根线束配合,因此势必会挤占电池包空间。此外,在 PACK 装配环节,非常依赖工人手工将端口固定在电池包上,工作效率以及良率均存在不稳定性。
与传统线束相比,FPC 在安全性、工艺灵活性、自动化生产等方面优势显著。此外还拥有高度集成、自动化组装、装配准确性、超薄厚度、超柔软度、轻量化等诸多优势。FPC 的可模块化及自动化生产特性,能够通过规模化生产降低生产成本,同时在关键元器件温感方面更可数十倍地降低成本,而且能进一步提高动力电池系统的组装效率。不仅如此,动力电池 FPC 还能在采集板上集成 NTC、保险丝,从而实现对动力电池实时监控温度和电压,并将采集数据反馈至 BMS,在超过设定的安全范围时,采集板保险丝将及时熔断,确保动力电池工作安全可靠。
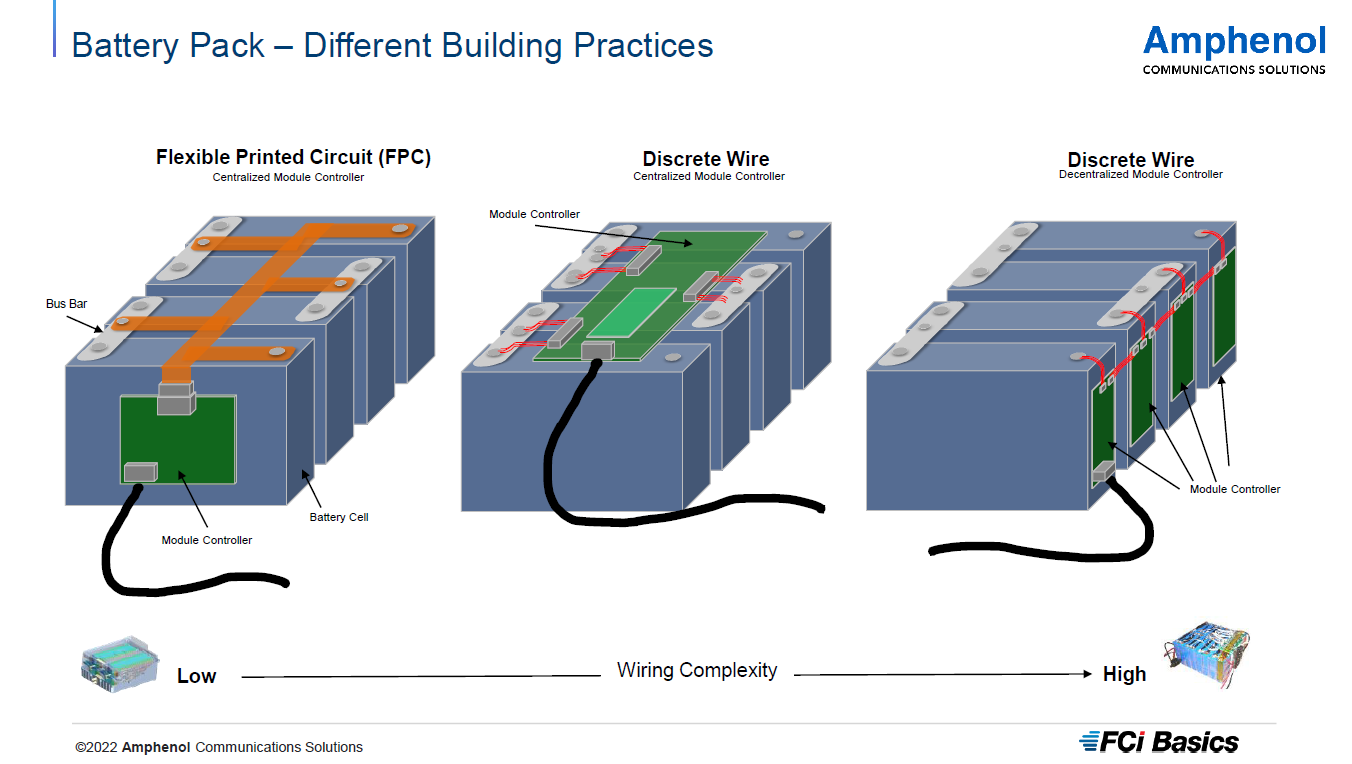
FPC VS 传统线束
图片来自:Amphenol
作为汽车用零部件,动力电池对 FPC 的安全性、稳定性、可靠性和耐久性提出了十分严格 的要求, 一方面,动力电池对 FPC 提出了耐温、耐压要求,因此 FPC 产品用料必须优质耐用;另一方面,动力电池用 FPC 需要具备监测电池电压、电流、温度等功能,同时需要根据的形状进行定制化生产,这也就决定了量产需要经过前期复杂的工序调整和严格的工艺测试。
近几年,在动力电池以及 FPC 厂商的共同推动下,通过不断改进工艺,FPC 在动力电池领域的导入环境得到极大改善 ,FPC 有望大批量导入行业。
文章引用来源:PCB 行业深度:通讯/消费电子/汽车齐 发力,FPC 替代传统线束前景可期-五矿证券[王少南]